- FE News»
- PPS News»
- Jul. 15, 2025
- Holiday Closing Notice [Summer 2025]
- Jun. 23, 2025
- Notice of Specification Change for ECHELON Zen-Xero Series Maintenance Bags
- Oct. 31, 2024
- [News Release R-1020] Release of "ECHELON Zen-Xero DYNAMIX”
- May. 15, 2024
- [News Release R-1019] Release of "ECHELON Ver.3.0”
- Oct. 02, 2023
- [News Release R-1018]Compound that achieves a genuine finish Full Renewal of “KATANA” Series
Aluminum Wheel Structure
Even among aluminum wheels, currently there are various products on the market and many types of surface treatments. When performing cleaning or coating, different materials and surface treatments will inform the chemicals you choose. Let us briefly look at some common surface treatments and constructions.
Paint Type
Just as with the body, spraying a “coating” onto the surface of the aluminum base forms a “film” with the finish color of the coating. By compounding coats, you can easily coat in a variety of colors, and because coating can be done at a relatively low cost it is the most common type of finish. Currently, there are many types of coating, and these vary in their durability and compatibility with different chemicals.
Metallic Coating
The most common type of coating is heat resistant metallic coating, which is applied with the same process as body paint. It is finished with a clear coat.
Maintenance
This type of coating is the easiest to work with: it has the highest resistance to chemicals for cleaning and maintenance, allowing use of all types of alkali and acidic products.
This type of coating is the easiest to work with: it has the highest resistance to chemicals for cleaning and maintenance, allowing use of all types of alkali and acidic products.
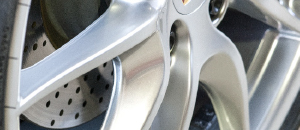
Hyper Coating
Luxury import vehicles and luxury brand wheels use a type of triple coating called Hyper Coating. This type of coating consists of a basecoat and solid color coat, after which a specially transparent metallic coating called Hyper Coating is applied, all of which is topped off with a clear coat. The coating’s color and luster change depending on how the light hits it, giving it a glossy and luxurious finish.
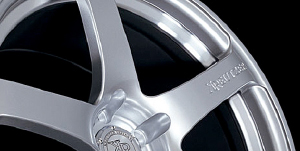
Maintenance
Just like normal metallic coatings, it handles various chemicals well, making it relatively easy to clean.
Just like normal metallic coatings, it handles various chemicals well, making it relatively easy to clean.
Sputter Coating
“Sputtering” is a popular kind of plating which gives the same luxurious finish as chrome. It is more expensive than normal coating, but because it gives the same luxurious feel as chrome at a more reasonable price it has seen frequent use in recent years. “Sputtering” is a plating process which affixes a shiny film in a vacuum using a chemical reaction. Generally it produces a silver mirror surface, but colored types exist as well.
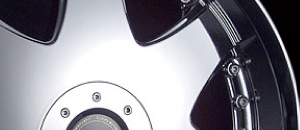
Maintenance
When maintaining or cleaning the surface, it can be handled like a coated wheel if there is a clear coat over the topcoat. However, the sputter coating itself is extremely delicate, so alkali chemicals or iron dust removers must be used with care. In general, acidic chemicals should not be used.
When maintaining or cleaning the surface, it can be handled like a coated wheel if there is a clear coat over the topcoat. However, the sputter coating itself is extremely delicate, so alkali chemicals or iron dust removers must be used with care. In general, acidic chemicals should not be used.
Cutting Type Machined
After the surface undergoes a diamond cut process, a “clear coat” is applied to the aluminum surface. This type of finish allows the natural gloss of the aluminum to come through to the surface. Coating and chrome each have their own uniquely luxurious feel, and they have become extremely popular in recent years.
Maintenance
This finish can generally be cleaned and maintained like other types of coating. However, flying stones can cause chipping of the clear coat, which in turn leads to white rust*1, a color which tends to stand out clearly. If the clear coat is damaged, chemicals can seep in from that spot, possibly damaging the surface of the aluminum. Please be careful.
*1: White rust is a type of rust caused by the oxidation of aluminum. Due to the properties of aluminum, if the coating surface is cracked and air comes into direct contact with the metal, it will certainly rust. It is difficult to remove with chemicals. Generally, the only option is to scrape it off and recoat the surface.
This finish can generally be cleaned and maintained like other types of coating. However, flying stones can cause chipping of the clear coat, which in turn leads to white rust*1, a color which tends to stand out clearly. If the clear coat is damaged, chemicals can seep in from that spot, possibly damaging the surface of the aluminum. Please be careful.
*1: White rust is a type of rust caused by the oxidation of aluminum. Due to the properties of aluminum, if the coating surface is cracked and air comes into direct contact with the metal, it will certainly rust. It is difficult to remove with chemicals. Generally, the only option is to scrape it off and recoat the surface.
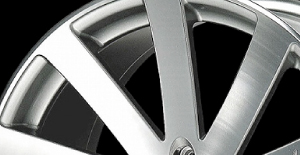
Alumite Type Alumite
“Alumite” is a colored finish which makes the aluminum look transparent. Although it is similar to the chrome plating process, “electroplating” uses the reaction at the cathode while “alumite” uses the reaction at the anode, reacting the surface of the aluminum itself to create a film of oxidation. In other words, because it is a film of oxidation (it starts as a membrane of rust), rust and other corrosion will not progress into the aluminum. This surface processing creates an exterior which stands the test of time. Furthermore, it is harder than plain aluminum and has excellent scratch resistance. However, if the bare aluminum becomes exposed due to a crack or scratch, corrosion can begin from that area.
Maintenance
Just like with chrome, this finish requires very delicate cleaning. Alumite can have varying quality even among products of the same price. Inferior products can sometimes lose their color simply by being cleaned with an alkaline cleaner. Please be careful.
Just like with chrome, this finish requires very delicate cleaning. Alumite can have varying quality even among products of the same price. Inferior products can sometimes lose their color simply by being cleaned with an alkaline cleaner. Please be careful.
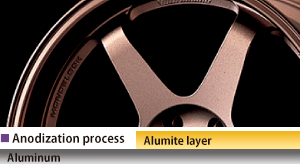
■What is alumite processing?
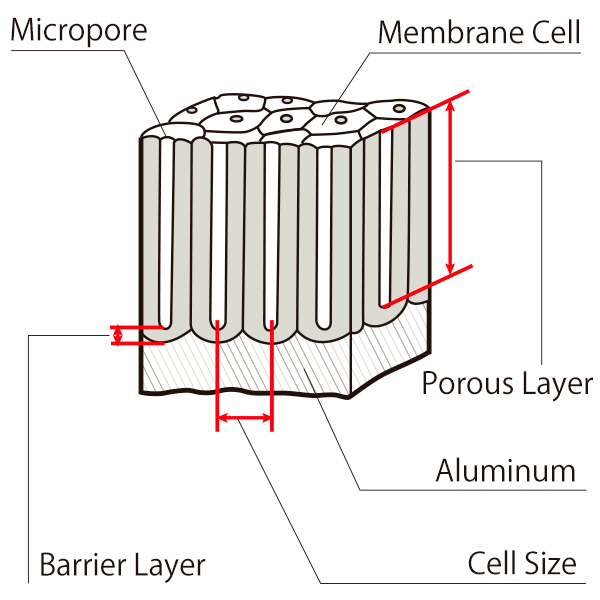
“Aluminum anodization (alumite)” is a surface process which aims to increase aluminum’s resistance to corrosion and wear while also decorating it with various colors. Electroplating is a surfacing process wherein the plating material is electrolyzed at the cathode and the metal ions in the electrolytic fluid are reduced and deposited at the anode. Alumite is the direct opposite of electroplating. In other words, aluminum is electrolyzed at the anode and oxidized. When iron or copper are used as an anode and oxidized, they simply dissolve into the electrolyzing fluid. However, if certain conditions are met, an aluminum anode which has been electrolyzed in the fluid will form a thick, uniquely shaped film of oxidation on its surface.
Chromium Plated Type Chrome Plating
Applying a “chrome electroplating (cathode)” process to the aluminum’s surface gives a thin, mirror-like film of color. This color has a mirrored exterior and outstanding gloss, making it the most luxurious color available. It is a far more expensive color than coated or machined finishes. Plating processes take a base metal which is resistant to oxidation and apply a different metal on top, thereby supplementing the weaknesses of the base metal with an extremely strong surface film. However, once the outer layer is damaged it can easily peel off, making it highly susceptible to scratches and cracks.
Maintenance
Due to the characteristics of plating, if exterior develops damage such as pinholes or cracks due to flying gravel, the base aluminum will rust from that area and the plating will peel away. Daily maintenance is essential. Furthermore, heavily dirtied or damaged plating is difficult to maintain, and use of strong chemicals can have adverse effects. Please be extremely careful.
Due to the characteristics of plating, if exterior develops damage such as pinholes or cracks due to flying gravel, the base aluminum will rust from that area and the plating will peel away. Daily maintenance is essential. Furthermore, heavily dirtied or damaged plating is difficult to maintain, and use of strong chemicals can have adverse effects. Please be extremely careful.
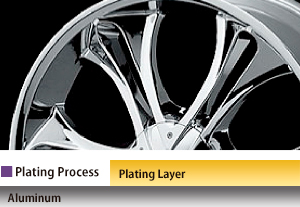