- FE News»
- PPS News»
- Jun. 23, 2025
- Notice of Specification Change for ECHELON Zen-Xero Series Maintenance Bags
- Oct. 31, 2024
- [News Release R-1020] Release of "ECHELON Zen-Xero DYNAMIX”
- May. 15, 2024
- [News Release R-1019] Release of "ECHELON Ver.3.0”
- Oct. 02, 2023
- [News Release R-1018]Compound that achieves a genuine finish Full Renewal of “KATANA” Series
- Jun. 27, 2023
- [News Release] A final finishing compound that achieves a beautiful wet gloss. "KATANA DARK-SHOT" is Released.
Headlight structure and materials
Headlights are made from either glass or resin. The most common type today uses polycarbonate resins. This is one of the strongest and most heat resistant types of plastic, but it also has weaknesses. We will begin by reviewing the material and structure.
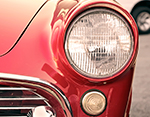
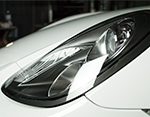
Material | Acrylic resin | Polycarbonate | Glass |
---|---|---|---|
Features | Glass-like transparency Excellent durability |
Hard to break Does not easily burn |
Scratch-resistant High durability Nonflammable |
Weaknesses | Easily deforms at high temperatures Flammable |
Scratches easily Poor weather resistance |
Breaks easily Difficult to manufacture Heavy |
Transparency | 93% | 86% | 92% |
Outdoor weather resistance | Good | Easily deteriorates due to ultraviolet rays | Very good |
Strength | High | Very high | Very low |
Surface hardness | About 2H–3H (pencil hardness) | About 1H–HB | About 1H–HB |
Flame resistance | Flammable | Self‐extinguishing | Nonflammable |
Relative density | 1.2 | 1.2 | 2.5 |
UV protection | Good | Good (absorbs UV rays) | Poor (none) |
Plastic materials and properties
PP (polypropylene)
PP has excellent moldability, allowing for a variety of molding methods. Among commodity plastics, PP is the lightest (relative density: ~0.9) and most heat-resistant type. It is resistant to chemicals such as acids, alkalis and organic solvents. Its physical properties can be reinforced with fillers, glass fibers, etc. Furthermore, like other polyolefin resins, it can be recycled. These strengths have made PP the most commonly used plastic for automobiles. PP has a very wide range of applications, including exterior parts like the bumper and door trim, interior parts like the instrument panel, electrical components and around the engine.
PE (polyethylene)
PE is mainly used for air ducts, fenders, fuel tanks and cushioning materials in vehicles, taking advantage of its lightness, low cost and resistance to low temperatures.
ABS resin
ABS resin is mainly used for interior parts like the instrument panel and exterior parts like the front grille, taking advantage of its excellent balance of physical properties, high-quality coloring, dimensional stability and moldability.
PVC (polyvinyl chloride)
While usage in the automotive industry has decreased in recent years owing to environmental concerns, PVC remains an indispensable material for automobiles due to its flexibility, texture and cost performance.
PA (polyamide, nylon)
PA is an engineering plastic most commonly used for interior parts due to its excellent heat resistance, chemical resistance, mechanical properties and moldability.
POM (polyacetal)
POM is an engineering plastic that exhibits excellent mechanical properties over the short and long term. It also has excellent moldability and a good balance of physical properties, including resistance to friction and wear and chemical resistance. POM has been in high demand in the automotive industry lately. It is used for many parts of the vehicle, including interior parts like steering wheels, exterior parts like windshield wipers and parts around the chassis like gas pedals.
PBT (polybutylene terephthalate)
PBT is becoming increasingly popular for automotive parts of every kind due to its outstanding balance of electrical properties, heat resistance, heat aging resistance, chemical resistance and resistance to friction and wear. It is frequently used for interior parts such as air outlets, exterior parts such as outer door handles and various electrical components.
PC (polycarbonate)
PC is an engineering plastic that excels in dimensional stability, resistance to low and high temperatures and mechanical properties such as transparency and impact resistance. It is often used for headlight lenses, meter covers and door handles.
Weaknesses of polycarbonate
Low surface hardness
Ordinary automobile paint has a hardness of 1H–2H, while polycarbonate is only about 1H–HB. This softness means that it scratches and clouds easily.
Poor solvent resistance
Polycarbonate is very weak against alkaline and organic solvents, which makes it prone to dissolution and cracking.
Poor UV resistance
Polycarbonate is highly susceptible to deterioration from ultraviolet rays, including yellowing and cracking. Prolonged exposure to ultraviolet rays causes the surface of polycarbonate resins to undergo a chemical change involving a rearrangement of its components. The product of this rearrangement appears yellow or reddish-brown, with a surface that absorbs ultraviolet rays. For that reason, after a certain point, polycarbonate stops changing in reaction to ultraviolet rays. This loss of transparency and yellow discoloration is called "yellowing."
Susceptibility to heat
Polycarbonate is superior to other plastic resins in terms of heat resistance, but when polishing a headlight with a polisher, the build up of heat may exceed its limits and lead to cracking. As such, caution is required.
Headlights: Contents
Related products