- FE News»
- PPS News»
- Jun. 23, 2025
- Notice of Specification Change for ECHELON Zen-Xero Series Maintenance Bags
- Oct. 31, 2024
- [News Release R-1020] Release of "ECHELON Zen-Xero DYNAMIX”
- May. 15, 2024
- [News Release R-1019] Release of "ECHELON Ver.3.0”
- Oct. 02, 2023
- [News Release R-1018]Compound that achieves a genuine finish Full Renewal of “KATANA” Series
- Jun. 27, 2023
- [News Release] A final finishing compound that achieves a beautiful wet gloss. "KATANA DARK-SHOT" is Released.
Coating application after polishing
Accordingly, there is a need to apply a new coating to replace the original hard coat. Candidates for this coating include the relatively easy to use hand-applied type and a painted type that is as similar as possible to the original hard coat. These effects of these coatings are drastic and unmistakable.
Types of coatings
Coatings for the vehicle body are the best known type of coating, but due to differences in composition and purpose, those coatings are not effective for headlights. The following properties are required for a headlight coating.1. Weather resistance against ultraviolet rays
2. Surface hardness on par with the hard coat
3. Excellent resistance to contaminants and solvents
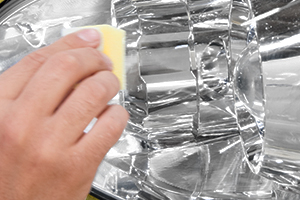
Methods for degreasing headlight lenses
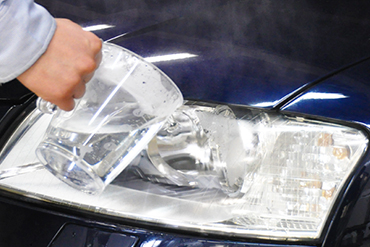
Zen-Xero Vario
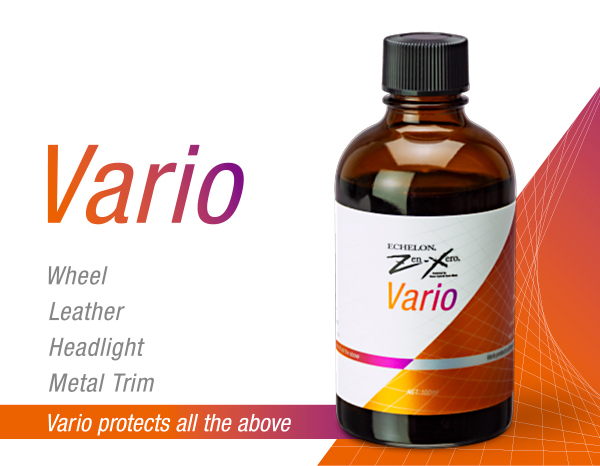
Durability:☆☆☆☆☆
Luster:☆☆☆☆☆
Now polycarbonate resin, rather than glass, is used for a material of headlights, and a various shapes of headlights exist. Headlights are important parts to determine the design of a vehicle. Deterioration and white turbidity of the hard coat layer of the surface of headlights are considered as a weak point of polycarbonate. It is common to polish and remove the hard coat with a water-resistant paper, buff the surface with compound to recover the transparency, and then apply a coating or paint on the surface to fix this problem. However, a product specially designed for headlights is needed to give the maximum effect to the material and conditions which are different from the painted surfaces. Zen-Xero Vario is formulated specially for headlights, and it prevents the deterioration of the coat itself and protects polycarbonate.
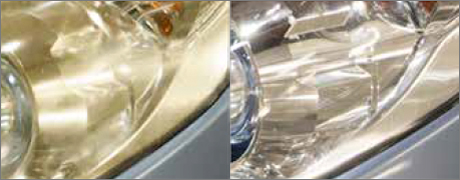
- before
- after
Weather Resistance Property Against Ultraviolet Rays
The hard coat originally on headlights uses the special kinds of paints which consider the effect of ultraviolet rays. Even so, it is impossible to avoid the effect completely, and it eventually gets deteriorated. When headlights are polished, ordinary auto body coatings do not have much resistance against ultraviolet rays, and polycarbonate gets deteriorated soon. However, this product forms a glass coat with strong siloxane bond which does not receive the excessive effect of ultraviolet rays and protects the polycarbonate surfaces for a long time.
Head Light Coating(thick type)
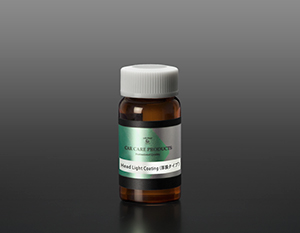
●Volume:20ml
Finish: ☆☆☆☆
Durability: ☆☆☆
Lens Reformer2

●Set contents:Main agent ・hardener
2. Improves the appearance of the vehicle by restoring the transparency and gloss of the headlights.
3. Maintains the appearance of the vehicle for a long period with excellent weather resistance.
4. These environmentally friendly products contain no substances subject to PRTR laws or the Ordinance on Prevention of Hazards Due to Specified Chemical Substances.
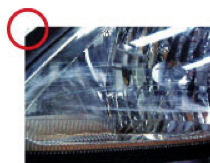
Repairable scratches
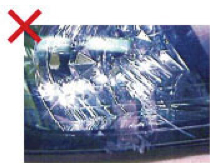
Unrepairable cracks
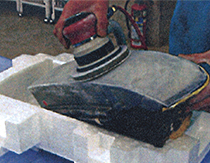
1. To completely remove scratches, sand the surface in stages, starting with P320 sand paper and ending with P2000 sand paper. This will completely remove the hard coat.
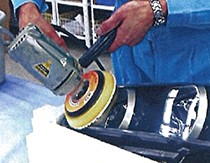
2. To remove sand paper marks, polish it in stages with a compound until the surface is completely transparent.
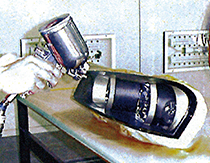
3. After degreasing, mask areas that do not require treatment and apply the primer. Let dry and then apply the final clear coat.
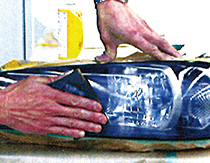
4. After forcibly drying the coating, remove any contaminants with sand paper, etc.
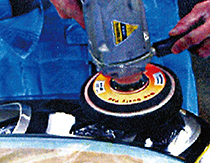
5. To remove sand paper marks, polish it in stages with a compound until the surface is completely transparent.
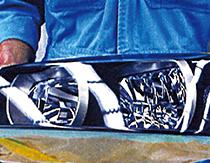
This takes approximately the same time as a normal coating process, but has been verified to remain effective for one to three years.