- FE News»
- PPS News»
- Oct. 31, 2024
- [News Release R-1020] Release of "ECHELON Zen-Xero DYNAMIX”
- May. 15, 2024
- [News Release R-1019] Release of "ECHELON Ver.3.0”
- Oct. 02, 2023
- [News Release R-1018]Compound that achieves a genuine finish Full Renewal of “KATANA” Series
- Jun. 27, 2023
- [News Release] A final finishing compound that achieves a beautiful wet gloss. "KATANA DARK-SHOT" is Released.
- May. 22, 2023
- [News Release] Full renewal of buffing pad category Brand integrated into HAYABUSA
[News Release] Next-generation Abrasive that Uses the Ultra-precision Smoothing Technology of Silicon Wafer "Expeed® UNIACTIVE" is Released.
News Release R-1013
Next-generation Abrasive that Uses the Ultra-precision Smoothing Technology of Silicon WaferNote 1
"Expeed® UNIACTIVE"is Released.
Speed and Polish Feeling that Overturn the Conventional Wisdom of Polishing Compounds
FE TRADE Co., Ltd. will start offering "Expeed®︎ UNIACTIVE", a high-performance abrasive that uses ultra-precision smooth polishing technology of silicon wafers. This product is the next generation abrasive based on sub-micron polyhedral particles (hereinafter abbreviated as SPP Note 2 ) that are diverted from the ultra-precision smooth polishing technology of silicon wafers, which boast the highest flatness of all materials in the world. Even with a long throw polisher (RUPES, FLEX, etc.), you can polish in the same amount of time as with a rotary action polisher, and experience a polish feeling that defies conventional wisdom.
Note 1: A substrate material used for semiconductors and an ultra-flat, ultra-clean disk that boasts the highest flatness among all substances in the world and eliminates fine irregularities and fine particles to the limit, formed by slicing ingot made by crystallizing silicon with high purity to about 1 mm and polishing the surface to a mirror finish.
Note 2: Abbreviation for sub-micron polyhedral particles. High-performance abrasive particles made by forming uniform sub-micronized particles into polyhedra after the refining process, applying ultra-precision smooth polishing technology of silicon wafers.
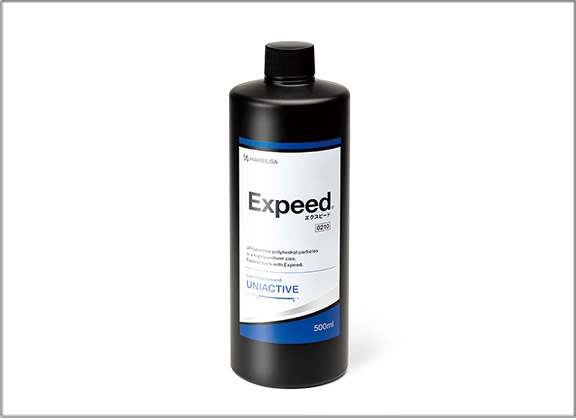
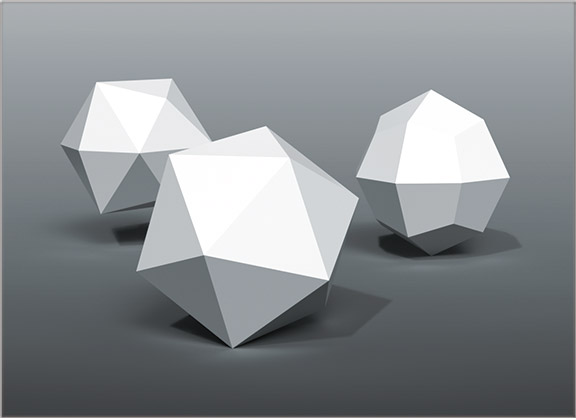
■ Background of the Launch
"Polishing is to make no extra scratches."With this concept, we have developed an advanced polishing compound with SPP as a base material that applies the world's highest level ultra-precision smooth polishing technology.The concept of polishing is to erase scratches with scratches and make them inconspicuous. As for conventional wide-range abrasives, the crushing type that aggregates particles to form large particles and changes each particle gradually into fine particles during the polishing process is the mainstream. Most of this type is generally recognized as a polishing compound with uniform particle size, but microscopic examination confirms that they are uneven in size and shape.Therefore, this time, we refocused on alumina oxide, which is generally used as a base for abrasives, and developed the new type polishing compound. While the error in the particle size of general abrasives is ± 100% or more, the particle size of this product is made uniform to 0.8 μ ± 20% through the refining process. Besides, by controlling the shape of the particles and making them polyhedra with the unique technology, high-performance abrasive particles with higher cutting force are formed.Using SPP refined through such a complicated manufacturing process as a base material, we have created a next-generation abrasive that has both polishing performance and finish.
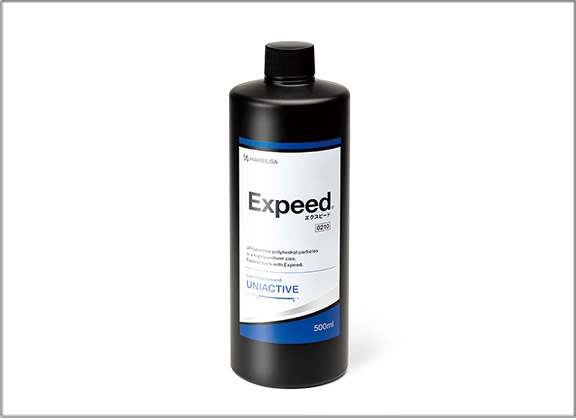
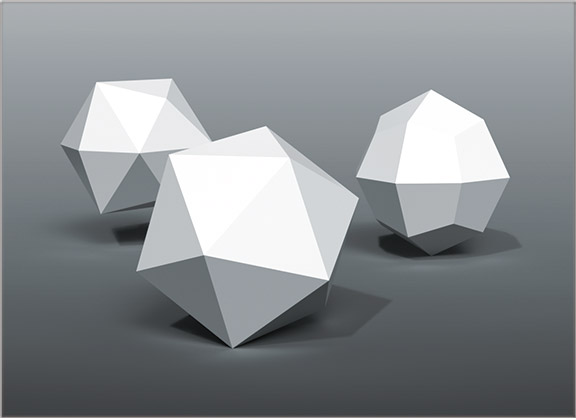
◎ Point1 Purified and sub-micronized abrasive particles (SPP)
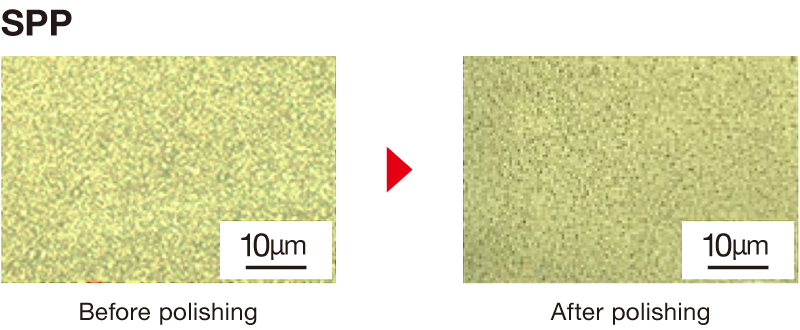
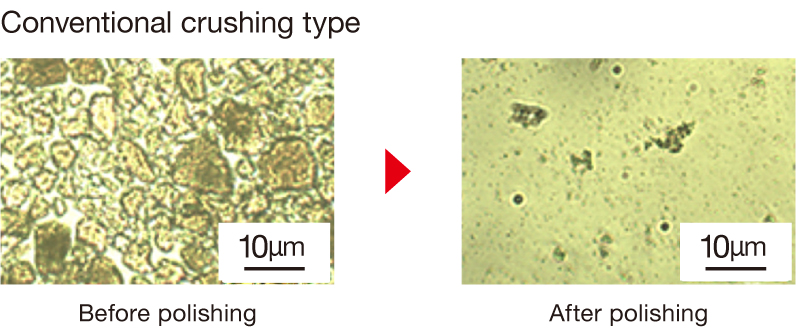
Due to the overwhelming uniformity of the abrasive particles of SPP, there is almost no change in particle size before and after polishing. In contrast, in general crushing type compound, there is a variation in size in micro units. Besides, the size of the abrasive particles of SPP show excellent uniformity and has a range of only about 1 µm from the reference value, whereas the particle size range of general crushing type is 10µm or more from the reference value.
◎ Point2 Polyhedral shape (unique particle shape that achieves both excellent polishing performance and finish)
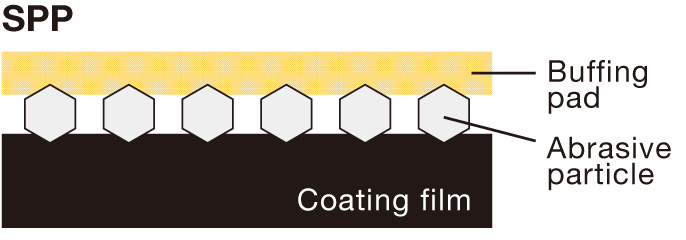
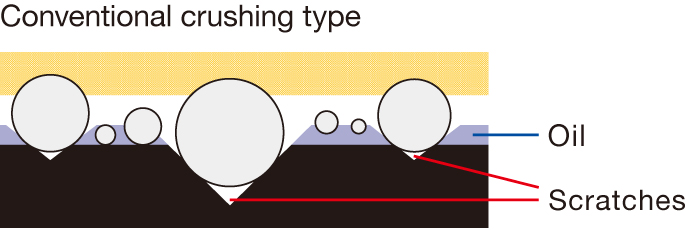
Not only the uniformity of the particle size, but also the polishing efficiency is improved by forming each of the abrasive particles into an intentional polyhedron and aligning them in the same shape.
■ Characteristics of the Product
1. Reduction of work time
Expeed® UNIACTIVEis extremely effective in working time not only with a conventional rotary action polisher, but also with a long throw polisher like RUPES. SPP (sub-micron polyhedral particles) with uniform particle size realizes stress-free polishing in a short time without causing unnecessary scratches.
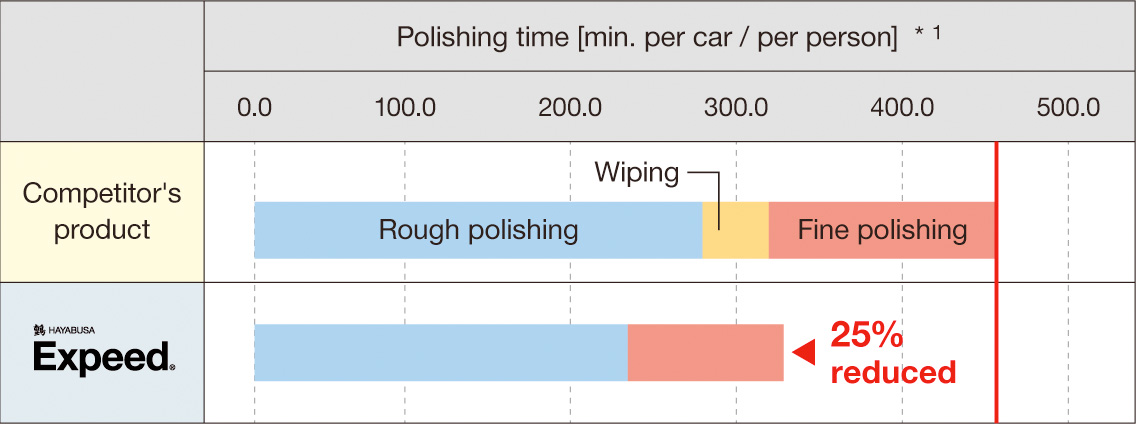
2. Compatible with self-healing functional paints, such as Scratch Shield
It is compatible with any types of coatings, and can perform accurate polishing* 2 even for Scratch Shield paint.
(* 2) When using a long throw polisher
3. Light polish feeling and clean finish without excessive oil
Due to the composition without excess components, there is no oil residue, so the finish is clean with a light polishing feel.
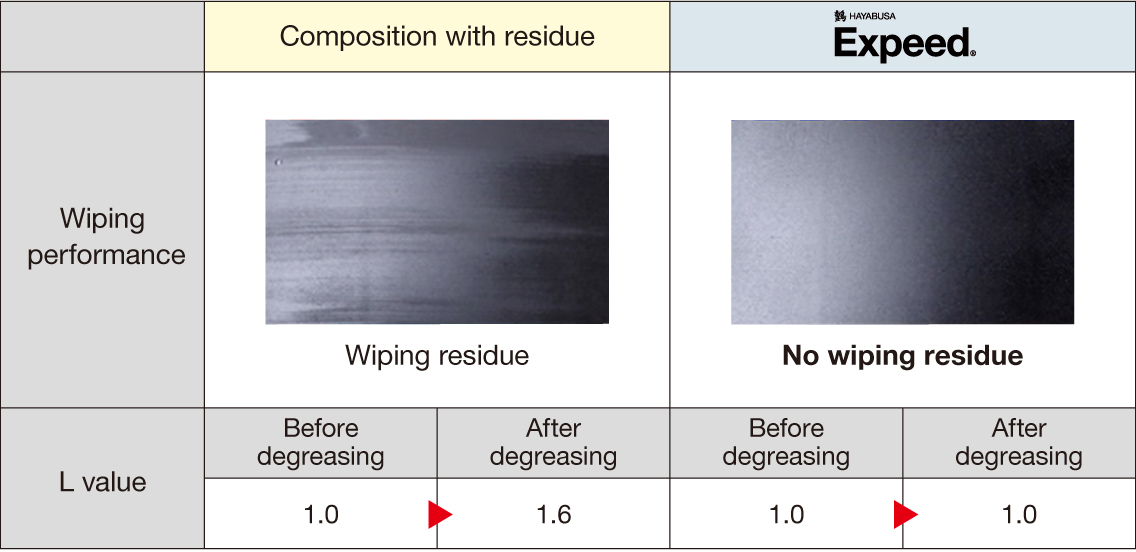
■ From the Section in Charge
The longer polishing time of a long throw polisher compared to a rotary polisher has long been a challenge in the auto detailing industry. We have taken this issue seriously, focusing on the base material of the polishing compound and working towards making rotary-like polishing time possible with a long throw polisher. This product may seem similar to existing products but is completely different because it has improved the purity of the same alumina oxide as before and pursued the unique particle shape. We are confident that we have reached a new standard, and will be pursuing the new values.
■ Product Summary
- [Volume] 500ml
- [Particles] Medium cut to finishing
- [Viscosity] 2
- [Liquid color] White
- [Characteristics] Non-silicone/wax-free, compatible with high-grade paint